Transforming inventory management into an efficient and responsive system can significantly boost a business’s operations. The Kanban inventory management system, hailing from Japanese manufacturing practices, is a powerful approach to achieving this efficiency. By visualizing work, limiting work in progress, and maximizing flow, this system helps companies respond quicker to customer demand while reducing waste. Below, we delve into what it takes to successfully implement Kanban within your business inventory management system.
Understanding Kanban Inventory Management and Its Benefits for Businesses
Kanban, meaning ‘visual signal’ or ‘card’ in Japanese, is an effective method for managing work by aligning demand with capacity. By implementing a Kanban inventory management system, businesses can visualize their workflow, identify bottlenecks, and minimize overproduction. This approach enhances inventory tracking, ensuring stock levels reflect actual consumption rates, leading to improved efficiency, reduced holding costs, and stronger supplier relationships.
Kanban fosters a collaborative work environment by promoting visibility and shared responsibility among team members. This engagement encourages a culture of continuous improvement, boosting morale and productivity. Customers also benefit from the system’s responsiveness, as timely and accurate order fulfillment enhances satisfaction and loyalty, making Kanban inventory a vital part of excellent customer service.
Essential Components of a Kanban System for Effective Implementation
A Kanban system is effective when it includes visual signals, physical spaces for specific materials or components, Work-In-Progress (WIP) limits, and Kanban boards. Visual signals represent tasks or inventory items, triggering actions within the production cycle. Physical spaces support an orderly flow of inventory items, enhancing visibility and ensuring materials are placed correctly.
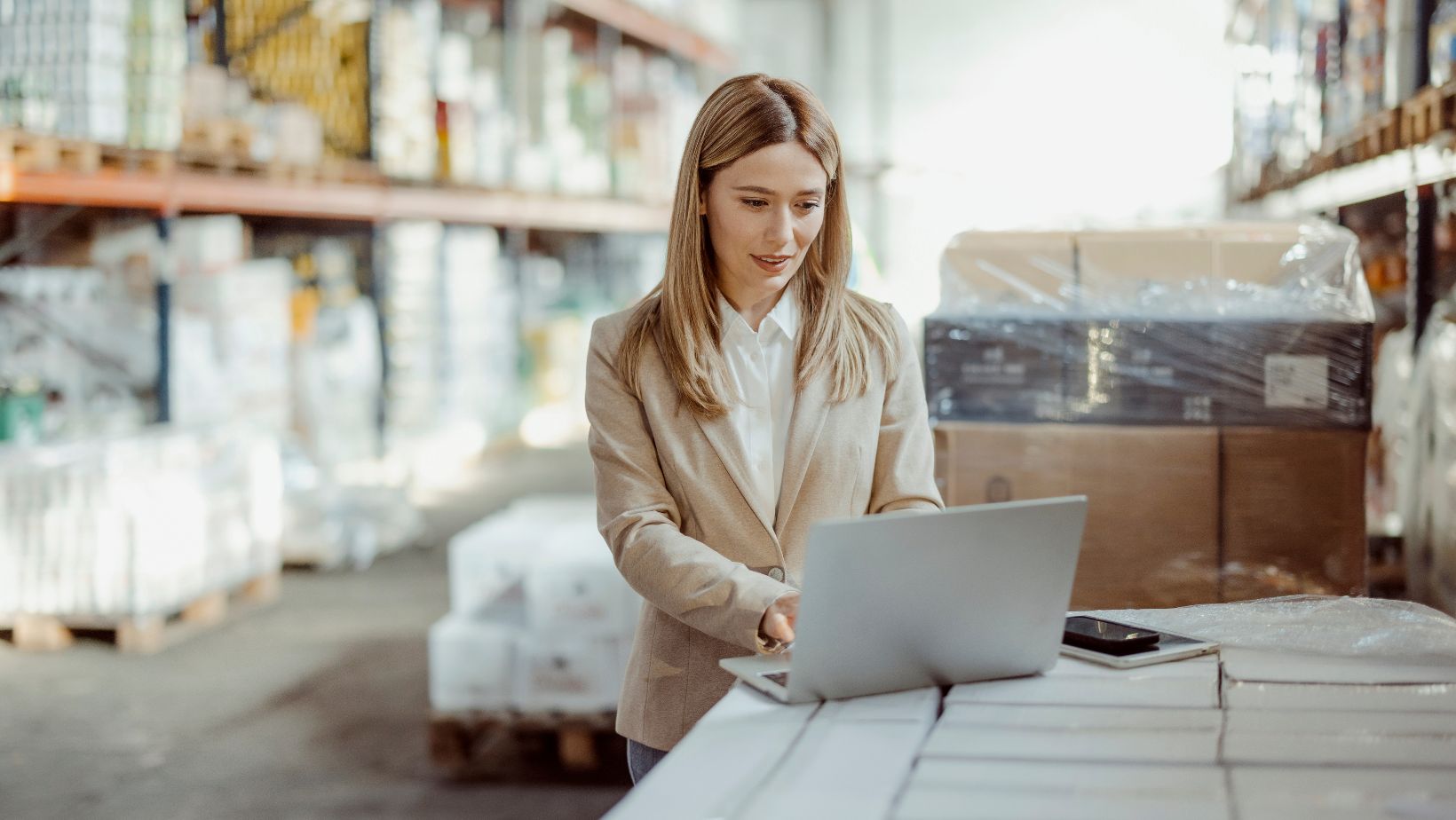
Work-In-Progress (WIP) limits prevent overproduction by limiting the number of tasks in any phase of the workflow. Kanban boards provide a central place for monitoring and managing task flow, allowing for rapid updates and adjustments, ensuring flexibility and adherence to Kanban principles.
Steps to Transition Your Inventory Management to the Kanban Methodology
The Kanban system is a method of inventory management that involves a systematic process of identifying and defining stages of the inventory process. This process, from procurement to delivery, is crucial for the visual representation of the inventory flow. The Kanban board, either a simple whiteboard or a sophisticated software solution, serves as the foundation of the system.
The implementation of WIP limits, which set maximum quantities for each inventory status, is a continuous process requiring careful observation and adjustment. The Kanban system is not just about tools and processes; it’s a cultural shift that requires training and employee involvement. Employees must understand the Kanban methodology, their roles within it, and be empowered to contribute to its ongoing optimization.
Leveraging Technology for Kanban System Efficiency and Real-Time Tracking
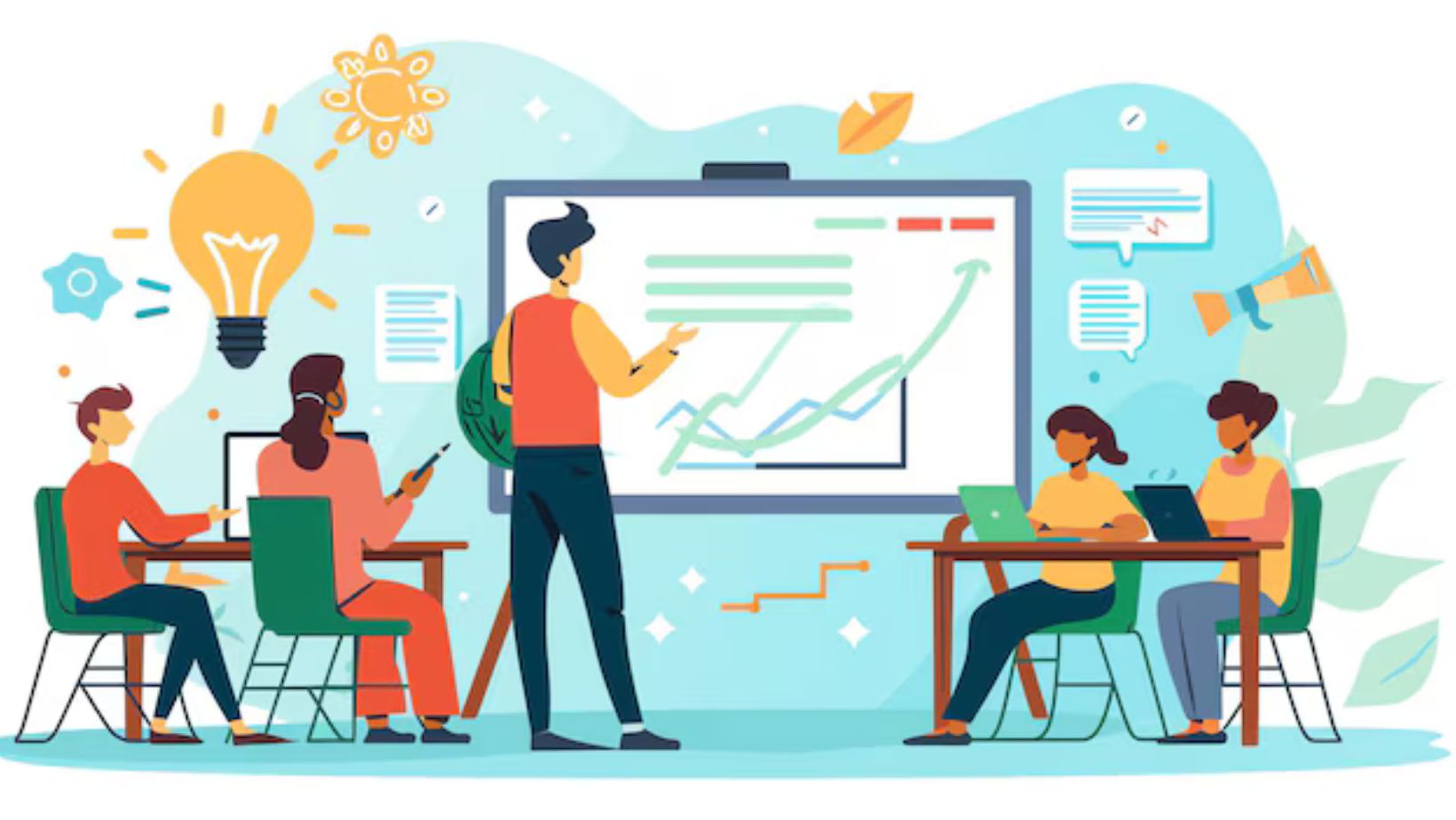
In today’s fast-paced business environment, a Kanban system’s efficiency is crucial. Digital Kanban solutions provide real-time updates and analytics, ensuring stakeholders have immediate access to the latest information. Mobile technology allows team members to monitor tasks from anywhere, making it beneficial for businesses with multiple locations or frequent offsite activities. Integrating Kanban with other systems like enterprise resource planning or supply chain management software can streamline operations and minimize human error.
Automated notifications and orders minimize the risk of human error, while data collected through technology can provide valuable insights for continuous improvement. By analyzing trends in inventory movement and task completion times, businesses can identify areas for process enhancements and anticipate demand changes.
Measuring the Impact and Continuous Improvement in Kanban Inventory Management
The success of a Kanban system relies on measuring its impact through key performance indicators like inventory turnover rates, cycle times, and fill rates. Regular monitoring of these metrics helps in understanding performance and directing improvement efforts. Qualitative feedback from employees and customers also provides valuable insights into the system’s efficiency. Employee feedback helps identify practical difficulties and areas for refinement, while customer satisfaction levels indicate the system’s ability to meet delivery expectations.
Kanban philosophy emphasizes continuous improvement, with regular reviews of policies, procedures, and WIP limits to evolve with changing business conditions. Benchmarking against industry standards and competitors can guide further development. By understanding Kanban inventory management best practices, businesses can strive for excellence and set the pace in their respective industries.
Overall, the introduction of the Kanban inventory management system can be a transformative step for a business looking to refine operations and elevate customer service. With diligent implementation and ongoing adjustments, the system’s full potential can be harnessed to create an environment of efficiency and continuous improvement. All it takes is commitment to the process and a willingness to adapt and innovate.